Despite the importance of the mid-infrared (MIR) wavelength region for a wide range of application areas, current state-of-the-art sensing systems in the MIR tend to be large and delicate. This greatly hampers their deployment in real-world applications.
REDFINCH will harness the power of Photonic Integrated Circuits (PICs), using hybrid and monolithic integration of III-V diode and Interband Cascade/Quantum Cascade materials with silicon to create high performance, cost effective sensors. Integration creates extremely robust systems, in which discrete components are replaced by on-chip equivalents, giving a simultaneous improvement in ease of use and a reduction in cost. Silicon photonics leverages the advantages of high performance CMOS technology, providing low cost mass manufacture, high fidelity reproduction of designs, and access to high refractive index contrasts that enable high performance nanophotonics.
REDFINCH will realise three fully-integrated PIC-based chemical sensor demonstrators for:
Process gas analysis in refineries
In refineries conducting the fractional distillation of crude oil into various products of commercial use, the monitoring of process gases is of crucial importance. For example, refinery gas is released during the production of butane, diesel and gasoline amongst others. Refinery gas is a mixture of multiple gases, consisting mainly of non-condensed hydrocarbon gases, C1 to C5. As the composition of refinery gas varies widely depending on the origin of crude oil, large-scale refining operations require fast decisions as the parameters of the process change.
Similarly, a major source of high-purity hydrogen gas is the process of steam reforming of light hydrocarbons (e.g. methane), employed in refineries. Hydrogen fuel cells are seeing intensive development as environmentally-friendly alternatives to petrol and diesel engines in transport applications. However, the purity of the produced hydrogen needs to be carefully monitored, as even a few tens of parts per million of impurities such as CO can poison the catalysts used in fuel cells, significantly degrading their performance.
The continuous monitoring and fast response time enabled by the REDFINCH sensor will greatly enhance process efficiency and output quality.
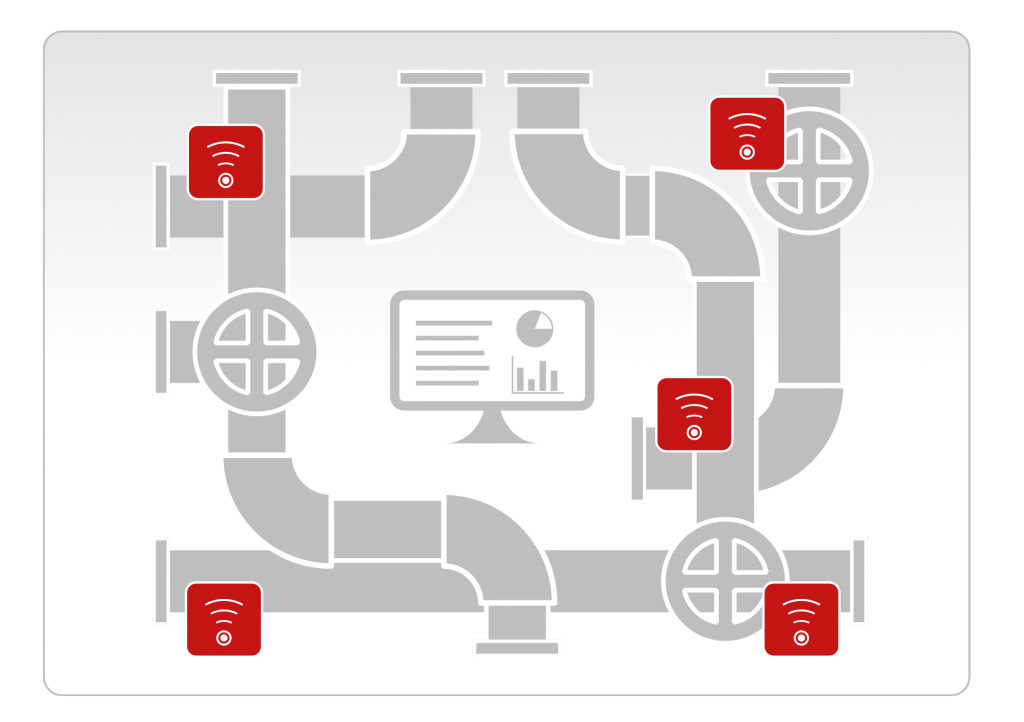
Gas leak detection in petrochemical plants and pipelines
The consumption of natural gas is steadily increasing worldwide; in Europe the construction of new pipelines and ports to deliver liquefied natural gas (LNG) from different sources to the European gas grid will establish reliable gas supply at low cost for the next decades. This gas grid will also serve as a huge storage system to compensate for the increasing share of fluctuating renewable energies in Europe. The infrastructure needs continuous monitoring, especially as it ages. Manual inspection, mainly using handheld portable sensors, requires a high amount of personnel and is very costly and time consuming.
Photonic Integrated Circuits with micro Photo-Acoustic Sensors (PIC-μPAS) developed in REDFINCH will be a key innovation for leak detection. These sensors will have a consumption of less than 10 W in continuous operation. For infrastructure monitoring, they will be operated in a slow pulse-burst mode. If a leak is detected the awareness of the sensor, i.e. the pulse frequency will be increased. By such methods, average power consumption is very low and the sensor could be battery-operated over a year or powered by an ambient energy harvester e.g. a solar cell. PIC-μPAS will be part of a wireless sensor network to monitor e.g. a refinery infrastructure.
Compared to existing sensors, they will be more sensitive, more specific and of higher dynamic range resulting in more reliable detection and less false alarms.
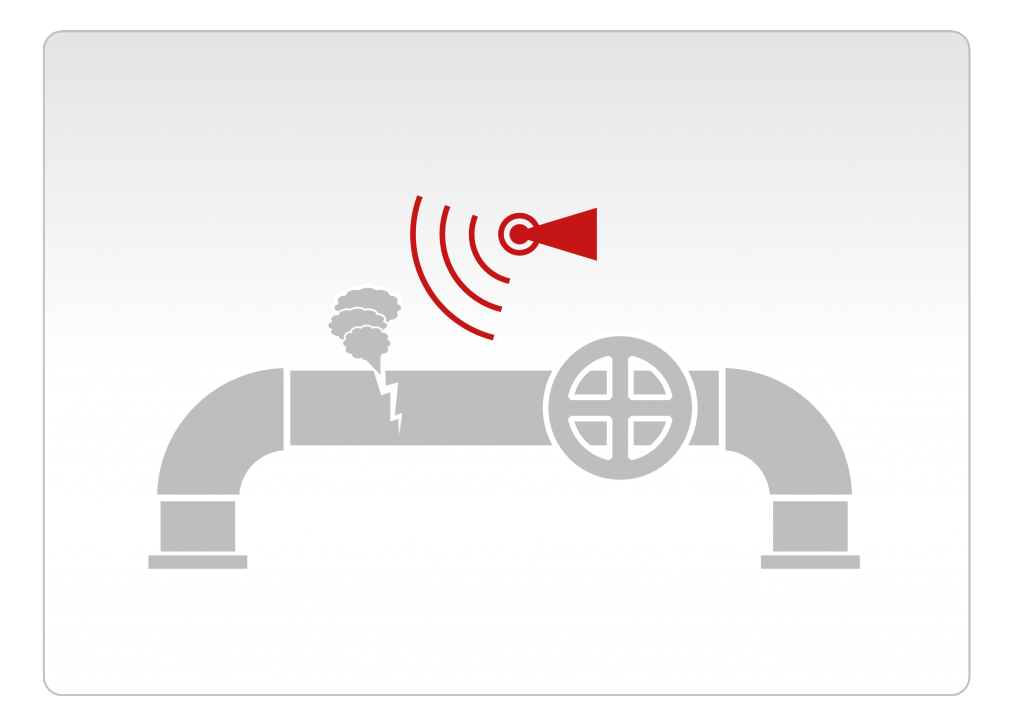
Protein analysis in liquids for the dairy industry
Milk production and processing is a multi-billion Euro industry. Farmers want to monitor the milk to better understand the health of their cattle and manage the herd. Dairies need to monitor the milk as the farmers are paid according to the constituents of the milk. Processors need to monitor the milk to quality control their products. Today nearly all milk monitoring is done offline through the taking of samples and the analysis of those in a lab – a slow, expensive process. State of the art milk analysers cannot differentiate between different types of proteins, they can only quantify the total protein content in a sample.
The REDFINCH protein sensor will enable analysis of the milk at the collection tanker, allowing efficient redirection and distribution of the consignment.
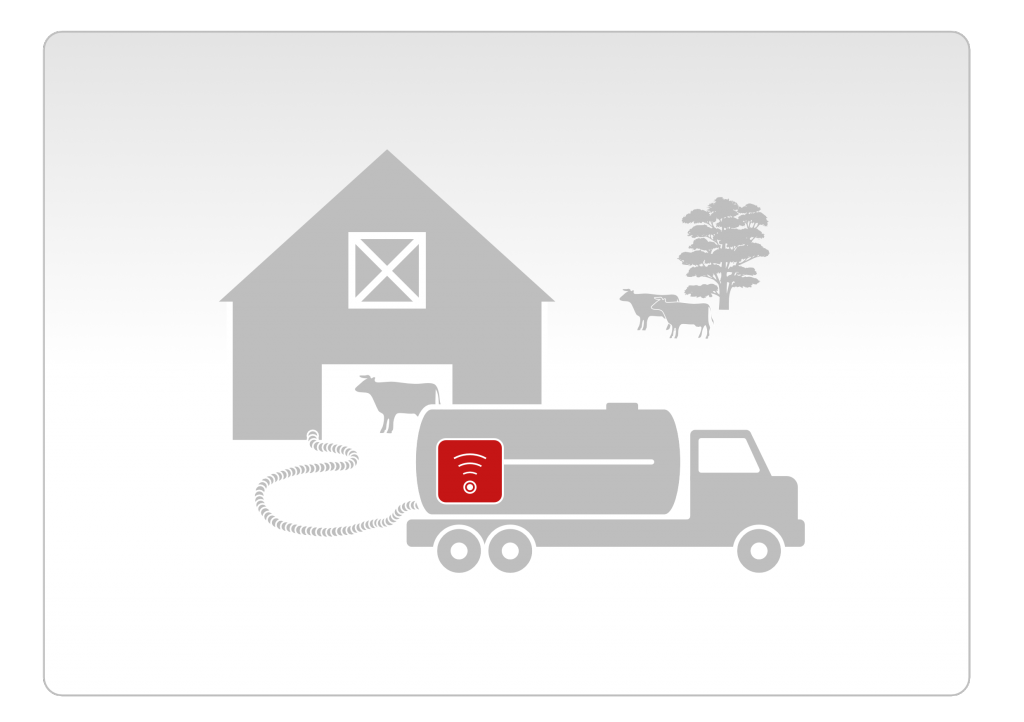